Hard Coatings: Revolutionizing Surface Protection across Industries
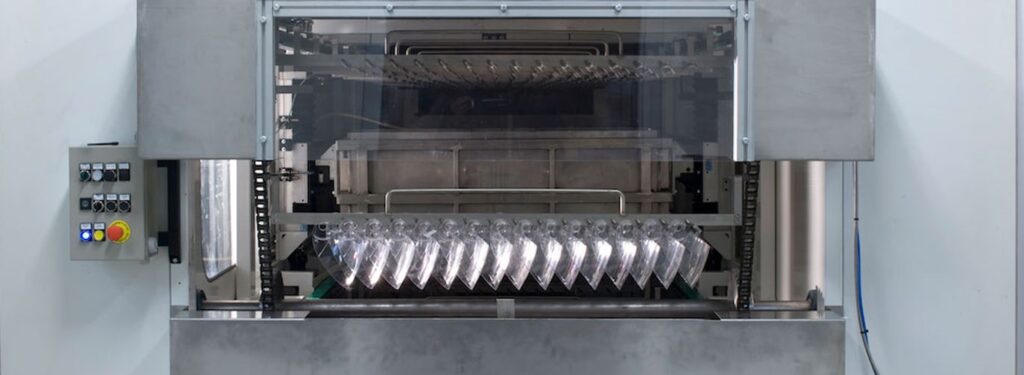
1. What is hard coating?
Hard coating is a method of applying a protective layer to the surface of a material. This coating is made from high-hardness polymer or metal compounds. After being applied to the material’s surface, the coating molecules bond tightly to the surface, enhancing hardness, durability, and environmental resistance, extending the material’s lifespan and reducing the need for replacements. As a result, hard coating is widely used in various industries. Depending on the application, different types of hard coating can be chosen, including anti-scratch coating, anti-fog coating, photochromic coating, and hydrophobic coating.
2. Types of hard coating
2.1. Anti-scratch coating
Anti-scratch coating is a method of applying a thin protective layer to the surface of a material to enhance its resistance to scratches, impacts, and abrasion. This coating is commonly used for materials like glass, plastic, metal, and ceramics,…
The composition of anti-scratch coating typically comprises high-hardness polymer or metal compounds. For instance, silicon dioxide (SiO2), the primary component of glass, offers exceptional scratch and chemical resistance. Titanium dioxide (TiO2) enhances the coating’s hardness and UV resistance, while zirconium dioxide (ZrO2) improves hardness and abrasion resistance. Other compounds like aluminum oxide and cerium oxide are also employed to bolster the protective effect.
Anti-scratch coating functions by creating a hard, smooth protective layer that minimizes direct contact between sharp objects and the material surface. During collisions or rubbing, the impact force is distributed evenly across the coating rather than concentrating on a single point.
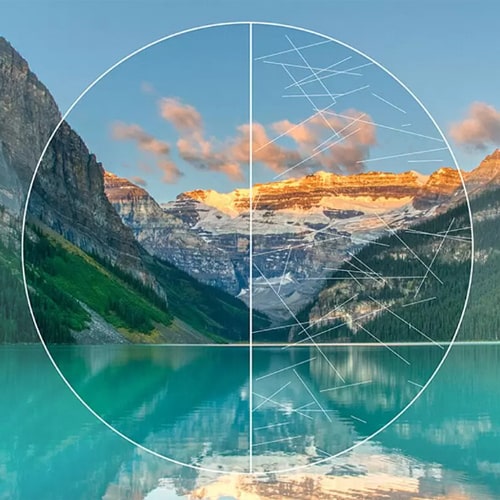
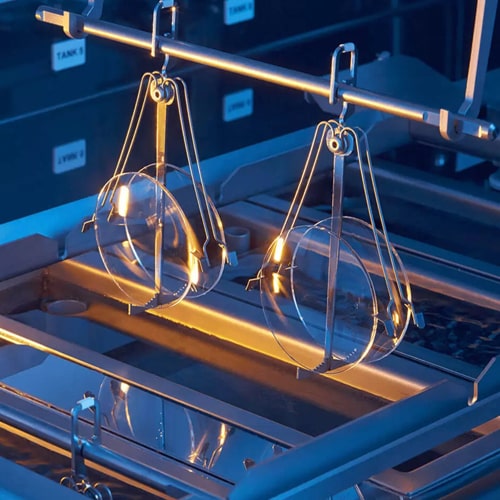
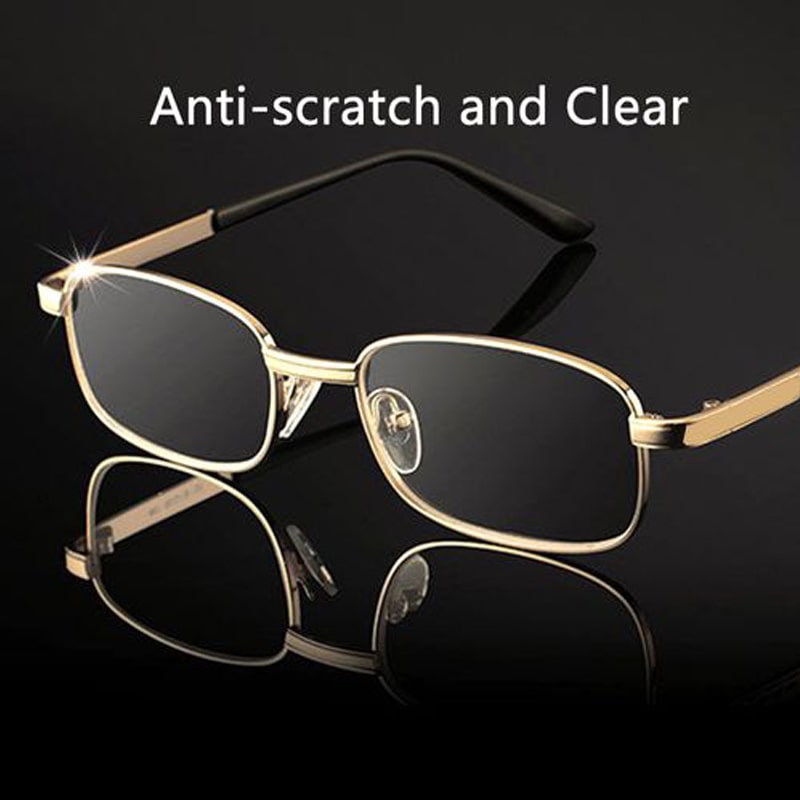
2.2. Anti-fog coating
Anti-fog coating is a method of applying a thin protective layer to the surface of a material to prevent the formation of condensation droplets caused by moisture. This coating is commonly used for materials like glass and plastic.
The composition of anti-fog coatings typically includes compounds such as: Polymers have the ability to alter their molecular structure upon exposure to moisture, creating tiny grooves on the material’s surface; surfactant reduce the surface tension of water, causing it to spread into microscopic droplets; Additives such as anti-UV agents, disinfectants, or other substances are added to enhance the coating’s effectiveness.
Anti-fog coatings function by altering the surface structure of the material, creating tiny grooves or indentations. When water vapor comes into contact with the surface, it spreads out into microscopic droplets instead of adhering as large beads. This allows water vapor to evaporate easily and prevents the material’s surface from becoming obscured.
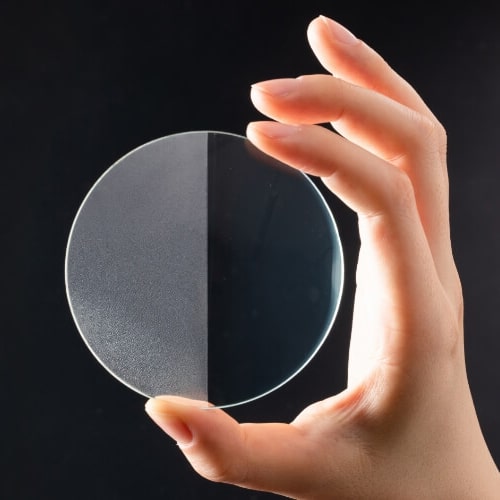
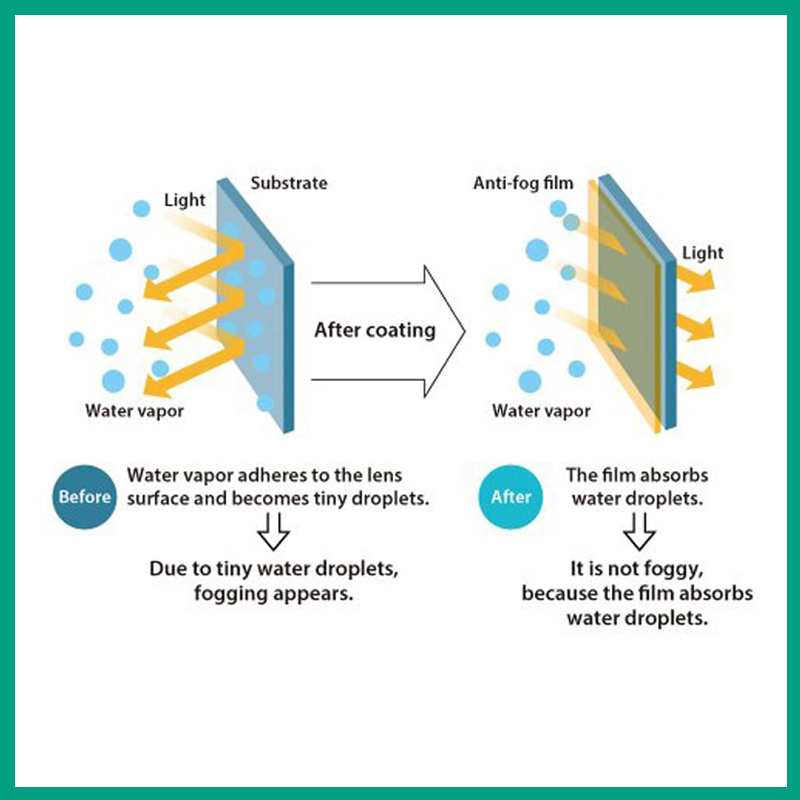
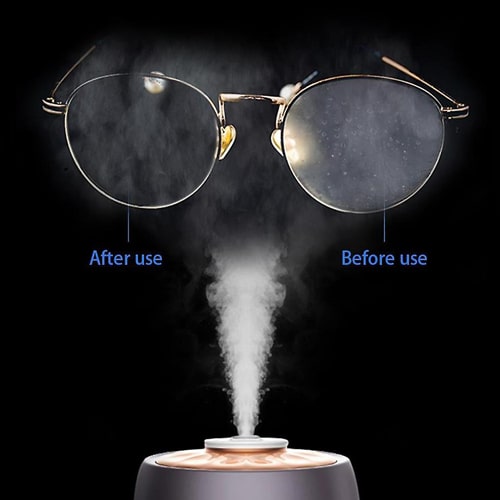
2.3. Photochromic coating
Photochromic coating is a method of applying a thin protective layer to the surface of eyeglasses or other materials. This coating has the ability to change color in response to UV rays from sunlight, adjusting the material’s tint and protecting the eyes from UV damage.
Photochromic coatings are composed of photosensitive materials that alter their structure upon exposure to UV radiation. Some common photosensitive compounds include: Spirobixan offers rapid color change and high UV resistance; naproxyl exhibits high durability and minimal temperature sensitivity; indenoquinoxaline enables transition to various colors, ranging from blue to brown. In addition to these photosensitive compounds, photochromic coatings also contain: Binders facilitate the adhesion of photosensitive materials to the lens surface. Additives enhance the overall performance of the coating, including UV absorbers, stabilizers, and other functional agents.
Photochromic coatings (lớp phủ chuyển sắc) function by altering the molecular structure of the material when exposed to UV rays from sunlight. In the absence of sunlight, the molecules in the photochromic coating exist in an “open” state, allowing light to pass through and the material to appear transparent. When sunlight is present, UV rays from the sun excite the molecules in the photochromic coating, causing them to transition to a “closed” state. This “closed” state has the ability to absorb light, hence the material changes color to a darker shade (typically gray or brown).
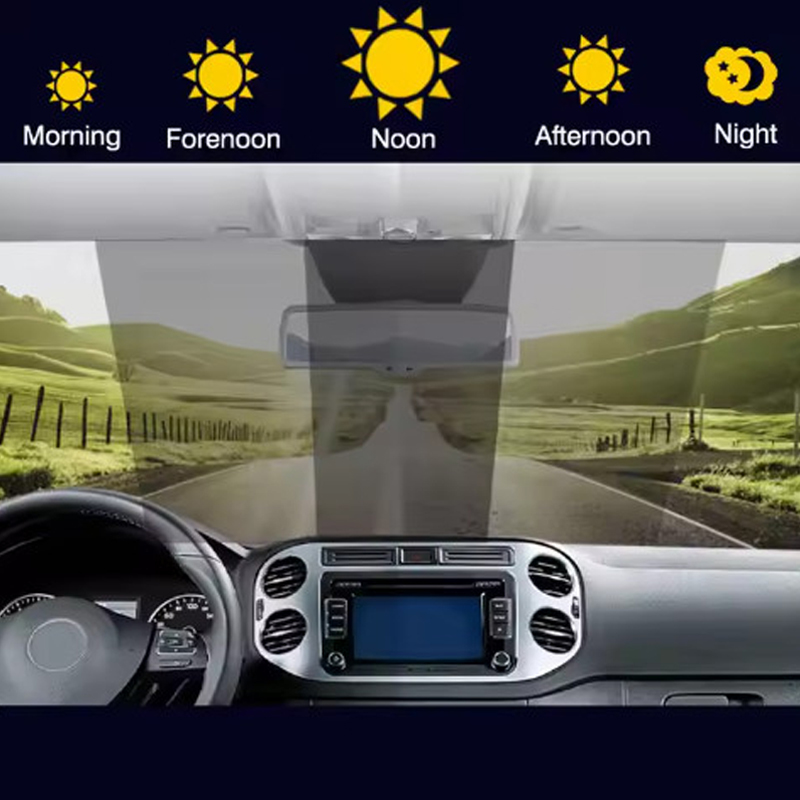
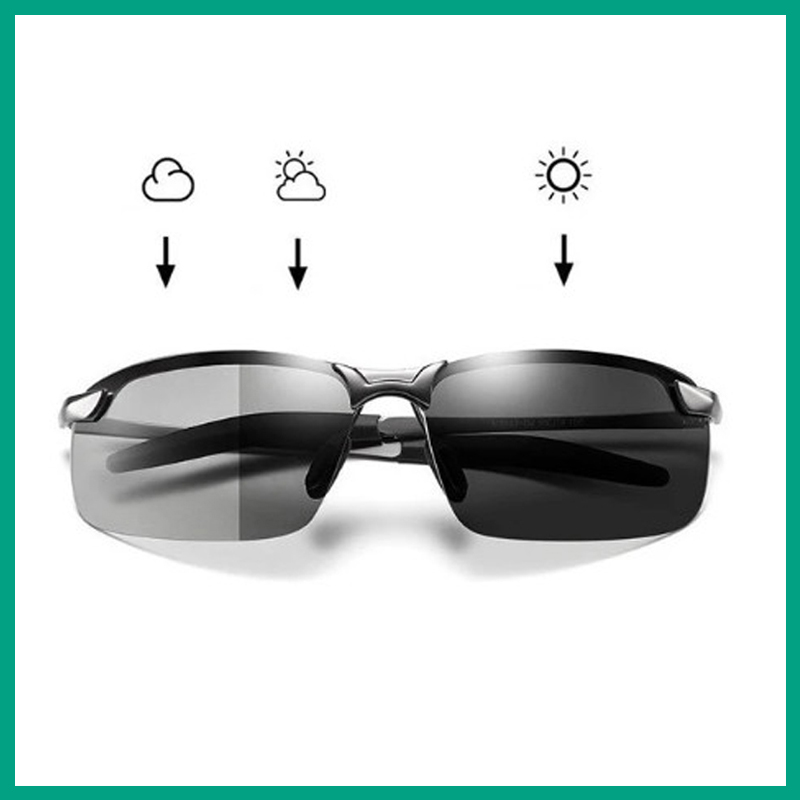
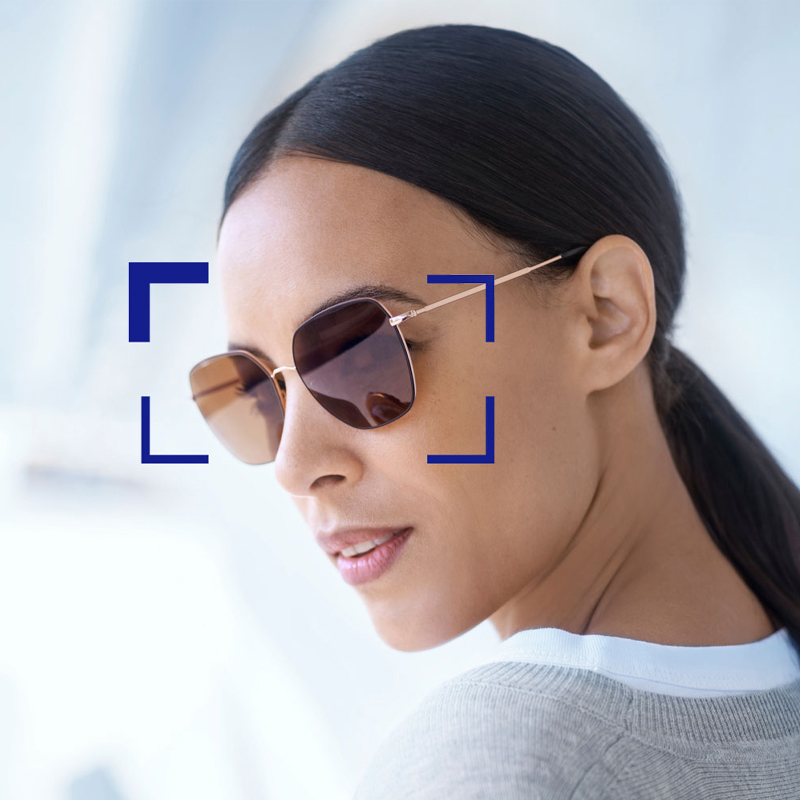
2.4. Hydrophobic coating
Hydrophobic coating is a special type of coating that is widely used in various industries due to its excellent water repellency and non-stick properties. As a result of its remarkable advantages, hydrophobic coatings are rapidly gaining popularity as a preferred surface protection solution.
Hydrophobic coatings are typically composed of the following components:
- Film-forming agents: Fluorocarbon polymers are the most common film-forming agents in hydrophobic coatings due to their unique molecular structure featuring carbon-fluorine bonds. This structure imparts exceptional chemical inertness and water repellency to the coating. Commonly used fluorocarbon polymers include Teflon (PTFE), Polyvinylidene fluoride (PVDF), and Ethylene tetrafluoroethylene (ETFE). Siloxanes: This class of silicone-based compounds containing silicon and oxygen forms a thin, elastic film that enhances the water repellency and non-stick properties of the coating.
- Additives: Plasticizers improve the flexibility of the coating, preventing cracking and peeling. Stabilizers protect the coating from degradation caused by sunlight, temperature fluctuations, and other environmental factors. Adhesives ensure strong adhesion of the coating to the substrate. Pigments impart the desired color to the coating.
- Solvents: Solvents dissolve the other coating components and facilitate the application of the coating to the surface. Common solvents include water, ethanol, and acetone.
- Additional additives: Nanoparticles enhance the coating’s properties, such as scratch resistance or UV protection. Antimicrobial agents prevent microbial growth on the coated surface. UV absorbers protect the coating from UV radiation-induced damage.
Hydrophobic coatings work based on the following principles: Firstly, altering the surface structure of the material: This involves creating an ultra-thin film with a smooth texture while minimizing surface roughness. This fills in the gaps on the surface, resulting in a significantly smoother surface. Secondly, water contact angle greater than 150 degrees: The water contact angle is the angle between the material surface and a water droplet. The larger the contact angle, the more easily the water droplet rolls off the surface. Finally, Water-sliding effect: When a water droplet comes into contact with a hydrophobic-coated surface, due to the contact angle being greater than 150 degrees, the water will form round beads that roll off the surface without sticking.
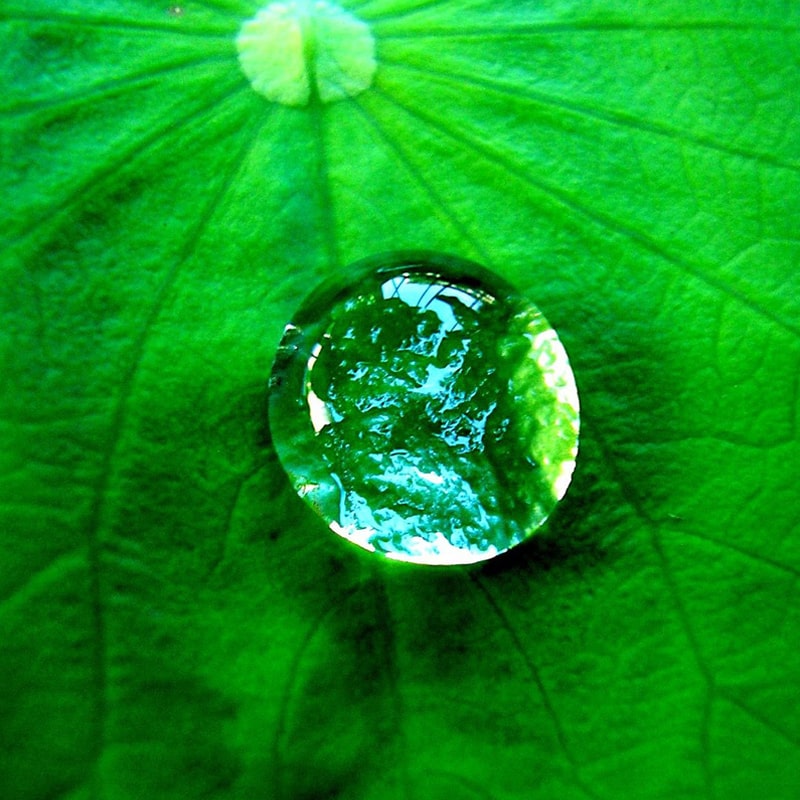
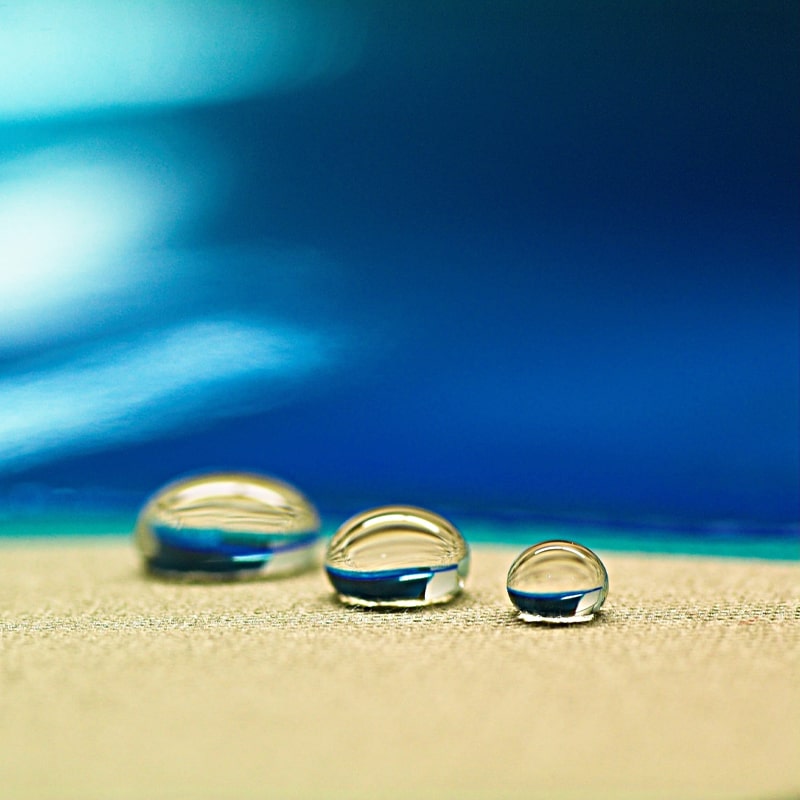
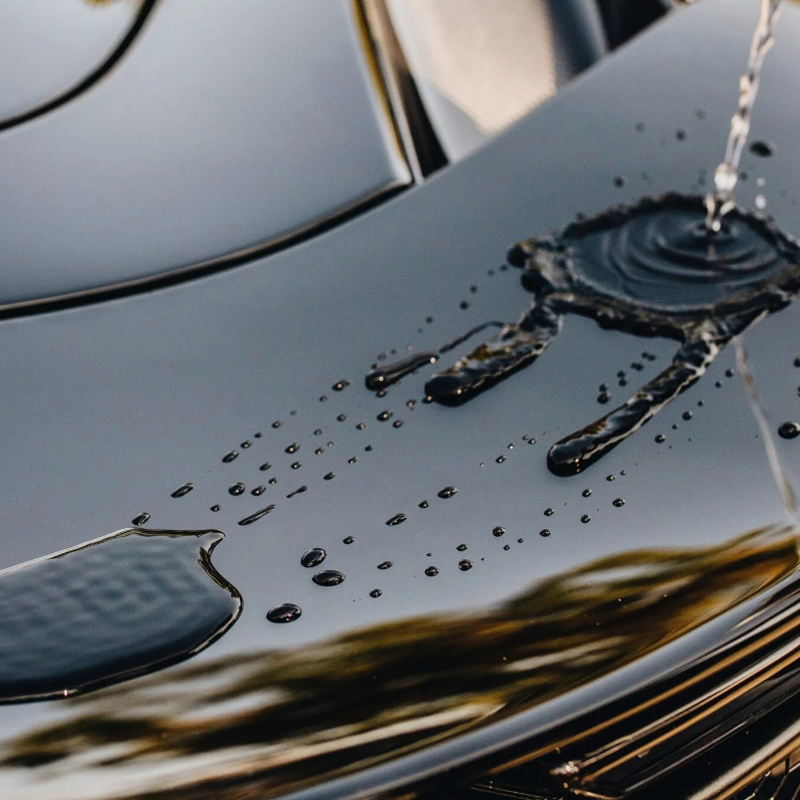
3. Methods of hard coating
3.1. Thermally Cured Coatings
This method utilizes polymers that crosslink when heated to a specific temperature. This crosslinking process forms a robust and durable polymer network that exhibits excellent resistance to chemical, mechanical, and environmental agents.
Advantages
High durability: Resistant to impact, scratches, abrasion, and chemicals. Excellent resistance to high temperatures, UV radiation, water, salt, and other chemicals. Good adhesion to a wide range of substrates, including metals, plastics, wood, and concrete.. Versatility: Can be applied using various methods, such as spraying, rolling, and dipping. High aesthetics: Can be produced in a variety of colors and effects to meet diverse aesthetic requirements.
Disadvantages
High-temperature requirement: The curing process of hard coatings necessitates high temperatures, resulting in substantial energy consumption and operational costs. Environmental impact: Certain hard coatings may release volatile organic compounds (VOCs) during the curing process, contributing to environmental pollution.
3.2. UV Cured Coatings
UV cured coatings are composed of prepolymers and UV-sensitive photoinitiators. Upon application to a substrate and exposure to UV radiation, the photoinitiators absorb UV light and initiate crosslinking reactions between the prepolymers. This crosslinking process results in the formation of a robust and durable polymer network that exhibits excellent resistance to chemical, mechanical, and environmental agents.
Advantages
Rapid curing: UV coatings can cure within seconds upon exposure to UV radiation, optimizing production time and minimizing costs. Excellent adhesion: UV coatings exhibit exceptional adhesion to a wide range of substrates, including metals, plastics, wood, and glass. Superior resistance: UV coatings demonstrate outstanding resistance to high temperatures, UV radiation, water, salt, and various chemicals. High versatility: UV coatings can be applied using diverse methods, including spraying, rolling, and dipping, catering to a wide range of application requirements. High aesthetics: UV coatings offer a wide range of colors and finishes, fulfilling diverse aesthetic demands. Safety and environmental friendliness: UV coatings are solvent-free and low in VOCs, ensuring user safety and environmental protection.
Disadvantages
Specialized UV curing equipment: The curing process of UV coatings necessitates specialized UV curing equipment, resulting in significant initial investment costs. Limited application constraints: UV coatings require application in a controlled environment away from direct sunlight to prevent premature crosslinking.
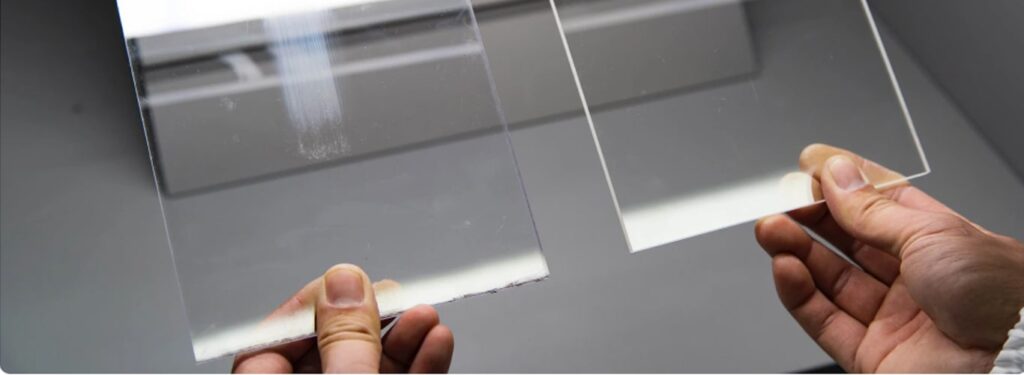
4. Applications of hard coating
4.1. Optics Applications
- Eyeglass Protection: Hard coatings safeguard eyeglasses from scratches, smudges, reflections, and UV rays, ensuring clear vision and protecting the eyes from harmful elements. This translates into enhanced visual performance, reduced eye strain, and long-lasting eyewear durability.
- Camera Lens Protection: Hard coatings protect camera lenses from scratches, dust, water, and other contaminants, preserving image sharpness and clarity. This translates into high-quality photographs, reduced lens maintenance, and extended lens lifespan.
- Microscope Lens Protection: Hard coatings safeguard microscope lenses from scratches, mold, chemicals, and other damage, ensuring high-precision and high-resolution imaging. This translates into accurate scientific data acquisition, reliable microscope performance, and extended lens lifespan.
- Optical Instrument Enhancement: Hard coatings enhance the performance and lifespan of optical instruments such as telescopes, binoculars, and microscopes. This translates into improved image quality, reduced light loss, and extended instrument durability.
4.2. Machining Applications
- Enhanced Tool Life: Hard coatings protect cutting edges and tool tips from wear and abrasion, increasing hardness and toughness. This enables high-speed, precise machining, significantly extending tool lifespan, reducing replacement costs, and optimizing production time.
- Improved Machining Efficiency: Hard coatings reduce friction between the tool and workpiece, minimizing heat generation. This leads to more efficient machining, saving energy, and improving product surface quality.
- Expanded Machining Capabilities: Hard coatings enable the machining of hard and difficult materials such as stainless steel, titanium alloys, and superalloys, meeting the ever-increasing demands of modern manufacturing.
4.3. Automotive Applications
- Engine and Transmission Protection: Hard coatings safeguard engine and transmission components from wear and corrosion, enhancing their durability, reducing noise, and improving engine performance. This translates into extended engine lifespan, smoother operation, and a quieter driving experience.
- Extended Drivetrain Component Life: By protecting gears, shafts, and bearings from wear, hard coatings significantly extend the lifespan of drivetrain components, minimizing breakdowns and contributing to a longer vehicle lifespan. This translates into reduced maintenance costs, improved vehicle reliability, and a more enjoyable driving experience.
- Reduced Fuel Consumption: Hard coatings can help reduce friction within the engine and drivetrain, leading to improved fuel efficiency and reduced emissions. This translates into lower fuel costs, a smaller environmental footprint, and a more sustainable driving experience.
4.4. Aerospace Applications
- Weight Reduction for Aircraft: Hard coatings enable significant weight reduction in aircraft components without compromising strength and performance. This leads to enhanced fuel efficiency, increased range, and reduced operational costs.
- Environmental Corrosion Resistance: Hard coatings protect aircraft components from harsh environments characterized by high humidity, extreme temperatures, and corrosive chemicals. This enhances aircraft durability, extends component lifespan, and improves overall flight safety.
- Improved Engine Performance: Hard coatings contribute to improved aircraft engine performance by reducing friction and wear, enhancing combustion efficiency, and optimizing airflow dynamics. This translates into increased thrust, reduced fuel consumption, and enhanced engine reliability.
4.5. Electronics Applications
- Wear and Corrosion Resistance: Hard coatings safeguard electronic components from wear and corrosion, significantly enhancing their durability and extending their lifespan. This translates into improved device reliability, reduced maintenance costs, and a longer product lifecycle.
- Enhanced Electrical Conductivity: Certain hard coatings possess excellent electrical conductivity properties, leading to improved performance and efficiency in electronic devices. This translates into reduced signal losses, optimized power distribution, and enhanced device functionality.
- Environmental Protection for Electronic Components: Hard coatings protect electronic components from harsh environmental factors such as dust, moisture, and corrosive chemicals. This enhances device reliability, ensures consistent performance, and extends the lifespan of electronic equipment.
4.6. Everyday Applications
- Enhanced Durability for Hand Tools: Hard coatings protect hand tools such as knives, scissors, and hammers from wear and corrosion, significantly extending their lifespan and durability. This translates into improved tool performance, reduced maintenance costs, and a more satisfying user experience.
- Jewelry and Accessory Protection: Hard coatings safeguard jewelry and accessories, preserving their shine and luster, preventing scratches, fading, and corrosion. This translates into long-lasting beauty, reduced tarnishing, and a more valuable appearance of personal belongings.
- Increased Durability for Frequently Touched Surfaces: Hard coatings protect frequently touched surfaces such as doorknobs, locks, and floors from scratches and wear, enhancing their durability and aesthetic appeal. This translates into a more presentable living space, reduced maintenance costs, and a longer lifespan for household fixtures.
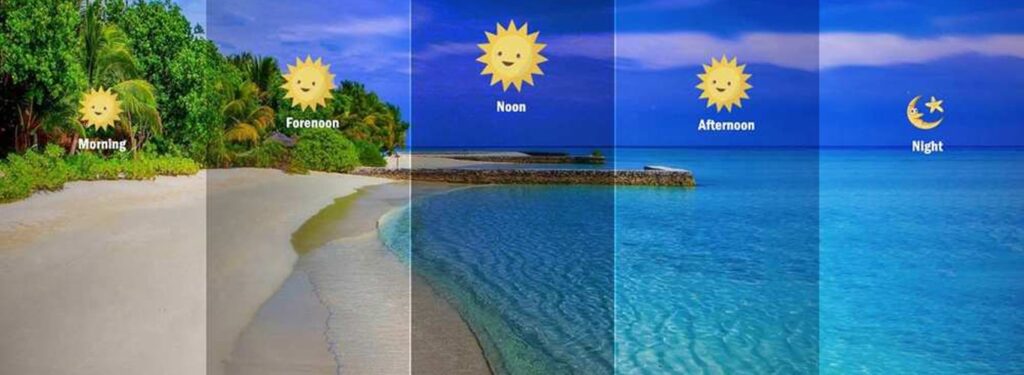
5. Contact us
Contact us today for a free consultation and quote
Email: ads.athardcoating@gmail.com
Mobile/Zalo: 0906 735 520
Hotline: 1900 9232