Vacuum Coating: The Secret to Enhancing Product Durability and Performance
1.What is Vacuum Coating?
Vacuum coating is a technology that applies a thin layer of material onto the surface of another material in a vacuum environment. This process is carried out by evaporating the coating material and depositing it onto the substrate surface.
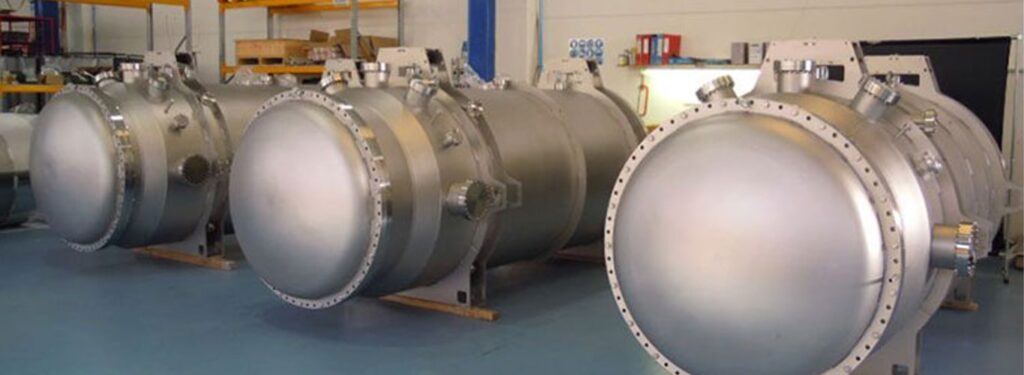
2. Vacuum Coating Process
2.1. Surface Cleaning
This is the most crucial step in the vacuum coating process. The surface must be completely cleaned of dust, grease, impurities, and rust layers to ensure optimal adhesion of the coating and achieve the desired quality. Here are the basic steps in the surface cleaning process for vacuum coating:
Determining Material Type
The first step is to identify the type of material to be cleaned. This step dictates the appropriate cleaning methods and chemicals. For example, metals are typically cleaned with acid solutions, while plastics may be cleaned with alkaline solutions or solvents.
Removing Dirt and Debris
Use mechanical methods such as brushing, sweeping, or blowing to remove dirt and debris from the surface. Vacuum cleaners or air compressors can be used to assist in the removal process. Ensure that the cleaning tools do not scratch the surface of the material.
Removing Grease
Grease can affect the adhesion of the coating and must be completely removed. Specialized cleaning solutions can be used to remove grease, following the manufacturer’s instructions for the cleaning solution.
Removing Rust (for Metals)
Rust is an oxide layer that forms on the surface of metals due to environmental exposure. It needs to be completely removed to ensure proper adhesion of the coating. Both chemical and mechanical methods can be used to remove rust. The chemical method involves using acid solutions to dissolve the rust. Ensure to use acid solutions at appropriate concentrations and follow safety measures. The mechanical method involves using tools such as wire brushes or grinders to remove rust. Use appropriate tools and handle them gently to avoid damaging the surface of the material.
Rinsing the Surface
After completing the above steps, the surface should be thoroughly rinsed with clean water to remove any remaining chemicals and impurities, ensuring they do not affect the coating.
Drying the Surface
The surface must be completely dried before proceeding with the vacuum coating. This can be done using a drying oven or allowing the surface to dry naturally in a clean environment.
Surface Treatment
Depending on the type of material and specific coating requirements, additional surface treatment steps may be necessary:
- Alkaline cleaning to remove impurities and oxides from metal surfaces.
- Phosphating to create a phosphate layer on the metal surface, enhancing coating adhesion.
- Anodizing to form an anodized oxide layer on aluminum surfaces, increasing hardness and corrosion resistance.
Inspecting the Surface
After cleaning and treating the surface, it should be thoroughly inspected to ensure it is completely clean and free of impurities. This can be done visually, with a microscope, or using adhesion measurement methods.
2.2. Creating a Vacuum Environment
This is a crucial step in the vacuum coating process, as it removes gases and impurities from the coating chamber to ensure the quality of the coating. The basic steps in creating a vacuum environment are:
Cleaning the Coating Chamber
The coating chamber must be cleaned of dust, grease, and other impurities before vacuuming. Use a clean cloth to wipe it down, wash with specialized cleaning solutions, and use a vacuum cleaner or air compressor to assist in cleaning.
Installing Components
Install the necessary components for the vacuum system, such as vacuum pumps, control valves, pressure measurement systems, and gas lines.
Creating the Vacuum
Start the vacuum pump and begin removing air from the coating chamber. The pressure in the chamber will gradually decrease over time. Monitor the pressure using the pressure measurement system and adjust the control valves to achieve the desired vacuum level.
Maintaining the Vacuum
After reaching the desired vacuum level, maintain it throughout the vacuum coating process. The vacuum pump needs to operate continuously to remove any leaked gases from the chamber. Monitor the pressure in the chamber and adjust the control valves as necessary.
Breaking the Vacuum
After completing the vacuum coating process, the vacuum must be broken to bring the chamber back to atmospheric pressure. Turn off the vacuum pump and open the control valves to allow air into the chamber. The pressure in the chamber will gradually increase until it reaches atmospheric pressure. Note that the vacuum creation process may vary depending on the specific vacuum system and the requirements of the vacuum coating process. Always follow safety measures when working with vacuum systems.
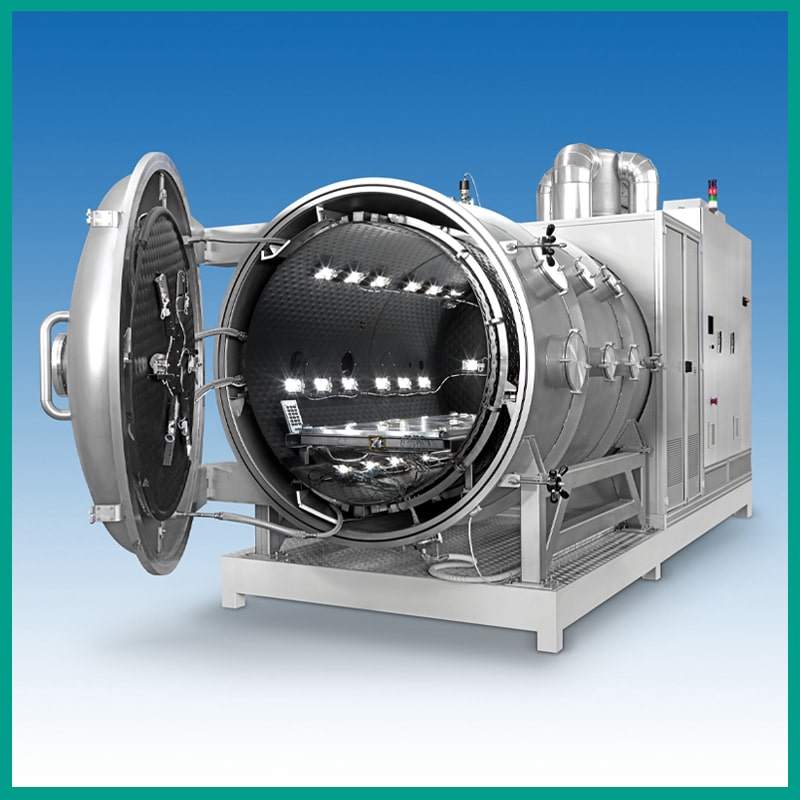
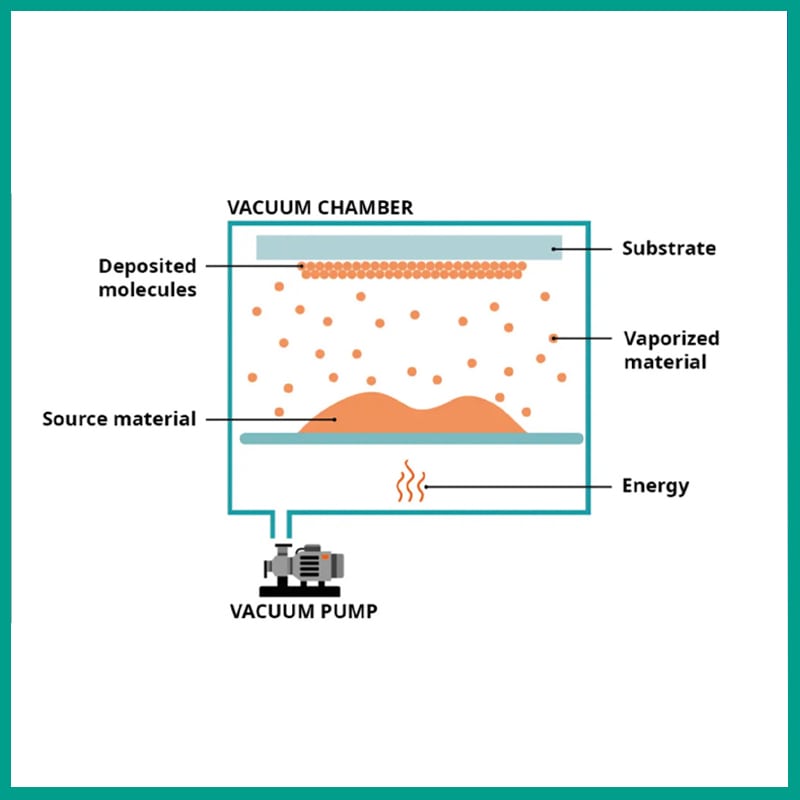
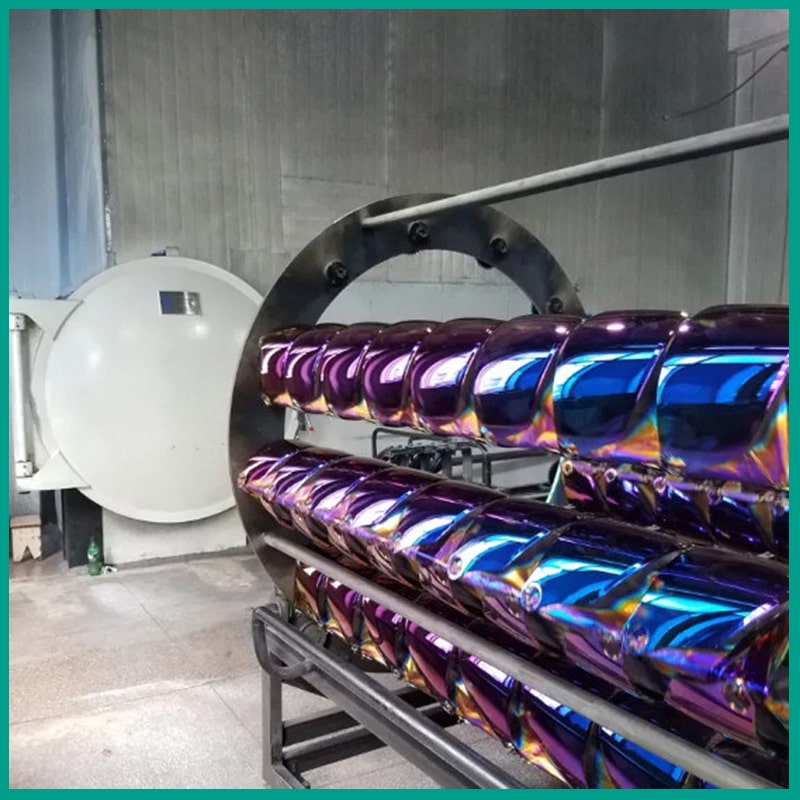
2.3. Evaporating the Coating Material
The coating material is heated to its evaporation temperature, typically using resistance heating or an electron beam. As the coating material evaporates, its atoms or molecules travel in straight lines within the vacuum chamber until they collide with the substrate surface. Common evaporation methods include:
Thermal Evaporation
The coating material is heated to its evaporation temperature using resistance heating or an electron beam. As the material evaporates, its atoms or molecules move in straight lines within the vacuum chamber until they collide with the substrate surface.
Reactive Evaporation
The coating material is evaporated in a reactive gas environment. When the atoms or molecules of the coating material collide with gas molecules, they can react to form a new compound, which then deposits on the substrate surface.
2.4. Material Deposition
Material deposition is the process of forming a thin coating on the surface of another material by allowing atoms or molecules of the coating material to move and adhere to that surface. In vacuum coating, material deposition occurs in a vacuum environment, which has a much lower pressure than atmospheric pressure. There are two main mechanisms of material deposition in vacuum coating:
Diffusion Deposition
The evaporated atoms or molecules of the coating material move randomly in straight lines within the vacuum chamber until they collide with the substrate surface. If the binding energy between the atoms or molecules and the substrate surface is sufficiently large, they will adhere to the surface and form a coating.
Assisted Deposition
External forces are used to assist the movement of the coating material’s atoms or molecules to the substrate surface. These forces can include electric fields, magnetic fields, gravitational forces, or collisions with other particles.
2.5. Controlling the Evaporation and Deposition Process
Precise control of the parameters during the evaporation and deposition process is crucial to producing a high-quality coating with the desired thickness, uniformity, and properties. Key factors to control include the evaporation source temperature, pressure in the vacuum chamber, distance between the evaporation source and the substrate, substrate tilt angle, substrate rotation speed, and evaporation time.
2.6. Finishing the Process
Once the desired coating thickness is achieved, the evaporation process is halted. The vacuum chamber is vented to return it to atmospheric pressure. The coated material is then removed from the chamber and inspected for quality.
3. Types of vacuum coating
3.1. Mirror Coating
Mirror coating is a technology that applies a thin layer onto the surface of materials to enhance light reflection capabilities. This technology is utilized across various fields such as glass, mirrors, medical equipment, and optics. Mirror coatings come in various colors, with light reflection intensity varying depending on the color and coating density.
3.2. Colored Coatings
Gold Coating
Gold coating is a technique using vacuum deposition to create a thin layer of coppery gold color on material surfaces. This coating resembles the lustrous color of bronze, imparting a luxurious, classical, and prestigious appearance to the surface.
Chameleon Coating
Chameleon coating is an advanced technique used to produce a glossy, iridescent layer on material surfaces. This process is conducted in a vacuum environment, utilizing seven different materials to achieve the desired color effects.
4. Applications of vacuum coating
4.1. Enhancing Hardness and Durability
- Mechanical Engineering Industry: Coating machine parts, cutting tools, shafts, etc., to resist scratches, abrasion, impact, chemicals, and high temperatures, thereby extending product lifespan.
- Automotive Industry: Coating pistons, camshafts, valves, etc., to enhance durability, reduce friction, and improve engine performance.
- Aerospace Industry: Coating engine fan blades, aircraft fuselages, etc., to resist corrosion and protect against harsh environmental conditions.
4.2. Oxidation Resistance
- Metal Industry: Coating metal components such as screws, bolts, clamps, etc., to prevent rust, corrosion, and protect surfaces from environmental impacts.
- Electronics Industry: Coating electronic circuit boards, connectors, etc., to protect against moisture, chemicals, and enhance reliability of devices.
- Medical Industry: Coating surgical instruments, medical devices, etc., to prevent bacterial contamination and ensure safety for patients.
4.3. Enhancing Aesthetic Appeal
- Fashion Industry: Coating jewelry, accessories, watches, etc., to create glossy, shimmering, and diverse color effects, imparting an elegant and attractive appearance.
- Household Industry: Coating knives, cutting boards, pots, pans, etc., to increase brightness, ease of cleaning, and add focal points to kitchen spaces.
- Furniture Industry: Coating interior decoration details, etc., to bring a sophisticated and modern aesthetic to living spaces.
4.4. Improving Performance
- Semiconductor Industry: Coating conductive and insulating layers on microchips to enhance efficiency, reduce noise, and save energy.
- Optoelectronic Industry: Coating anti-reflection layers to increase light transmission for solar panels, LED lights, improving energy conversion efficiency.
- Medical Industry: Coating antibacterial layers on medical instruments to reduce cross-contamination risks.
4.5. Other Applications
- Optical Coating: Coating anti-reflection layers to increase light transmission for lenses, improving image quality.
- Sensor Coating: Coating sensitive layers for light, gases, etc., to create precise and efficient sensors.
- Biomedical Coating: Coating functional layers for medical implants to enhance biocompatibility and reduce rejection risks.
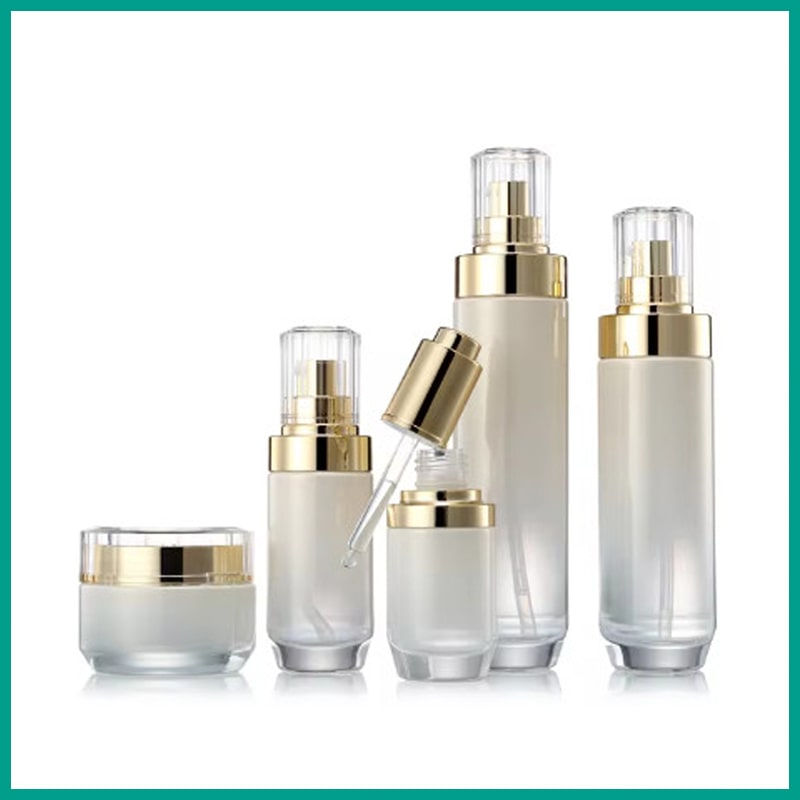
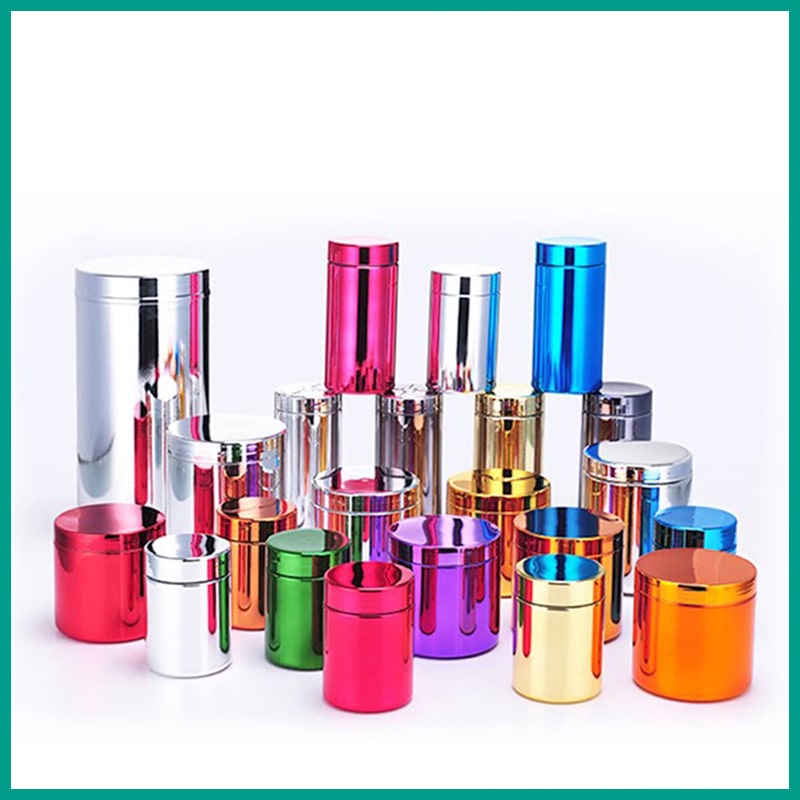
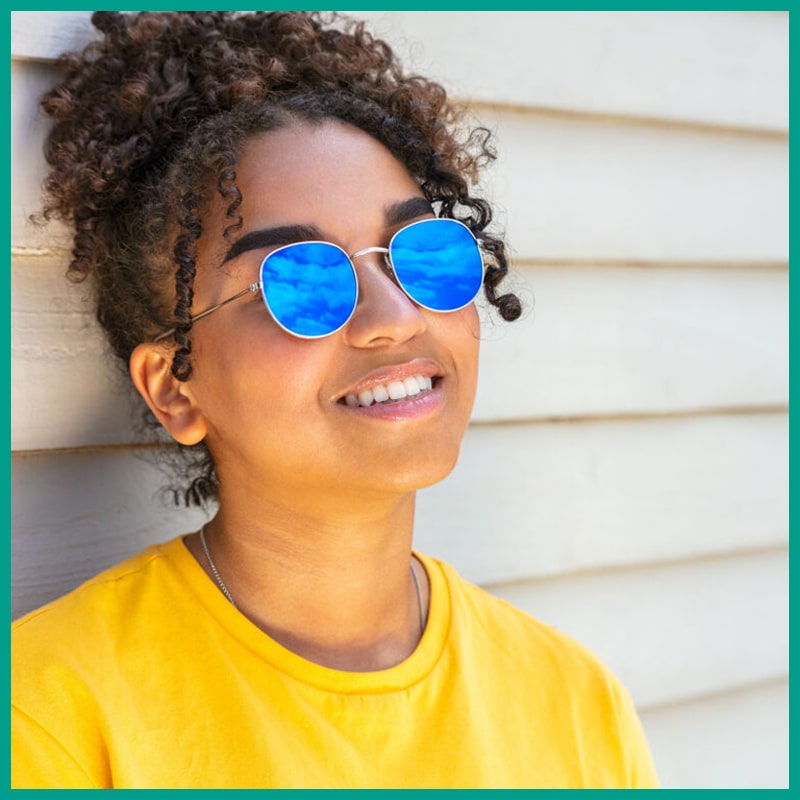
5. Contact us
Contact An Tran Hard Coating for a free consultation and quotation:
Email: ads.athardcoating@gmail.com
Mobile/Zalo: 0906 735 520
Hotline: 1900 9232